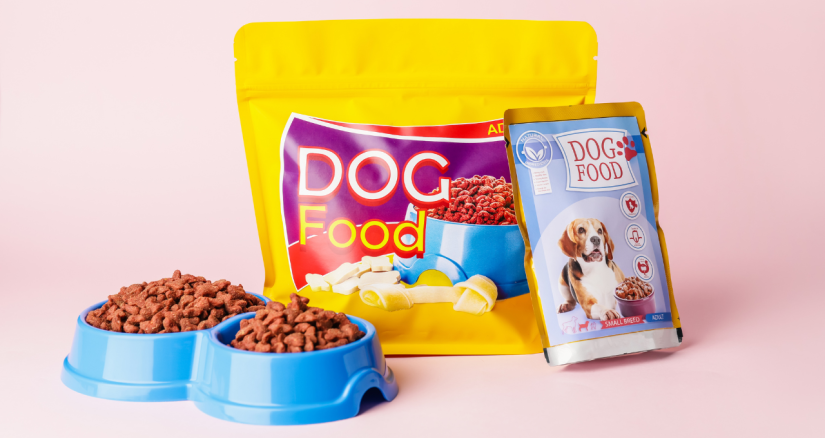
Nutrient Variability in Commercial Pet Foods
Pet owners want the best for their companions, and proper nutrition is paramount for keeping pets happy and healthy. Most pet owners leave the production of their pets’ diet to professionals and purchase commercially available pet food. Assuming these diets are labeled as “Complete and Balanced”, they should adhere to certain nutritional standards that are based on the species and life stage they are intended for. What does it mean to be “Complete and Balanced”? Do all foods labeled “Complete and Balanced” provide similar nutrition?
What is a nutrient requirement?
Before diving into nutrient variability, let’s first discuss what a nutrient requirement is. Nutritional standards are set by the Association of American Feed Control Officials (AAFCO), which are then enforced by the state’s regulatory body, or in the case of specific claims (ex. urinary diets), the FDA. Nutrient requirements help to ensure that food has the correct amount of each nutrient to keep pets healthy. At a basic level, these requirements are derived from scientific experiments and model-based approaches and generalized to the “average” animal. Much of this research is summarized in the publications by the National Research Council, which is then utilized by AAFCO and other authorities when implementing requirements.
Commercial pet food manufacturing
Like most commercial products, the manufacturing of pet foods is complex and involves many processes before it arrives on the shelf. These processes can alter the nutrient profile of the diet. The process begins with ingredient sourcing and formulation, where the formulator selects the ingredients to be used to make the food, and then formulates a diet to meet the specified nutrient requirements. A formulation is only as good, or accurate, as the ingredient nutrient profile it possesses. During production, ingredients are mixed, possibly extruded, and dried or retorted, and packaged to be sent to retail stores or consumers. In many cases, foods are designed to have a shelf-life between 18 and 24 months; however, the amount of time that elapses between manufacture and feeding can be quite variable. Each of the above steps ultimately influences the nutrient profile of the finished product.
Sources of error
1. Ingredient nutrient profiles
During formulation, certain assumptions must be made regarding the nutritional content of individual ingredients. For example, it may be assumed that the crude protein content of soybean meal is 47%. However, in reality, the crude protein content will vary, in some cases considerably. Factors such as plant growing season, harvest methods, processing methods, and storage conditions can all affect the content of various nutrients such as amino acids and vitamins.1-4 So, while the crude protein content may be assumed to be 47% during formulation, the actual amount will vary from batch to batch. Discrepancies between the value used during formulation and the true value will lead to errors in the nutrient profile of the finished product. For example, if the above soybean meal specification allows for ± 5% on crude protein, the actual value will range from 44.6% to 49.6%. If this ingredient is included in the diet at 30%, then the crude protein of the final product can be nearly 1% less than formulated just from variability in a single ingredient. While this may not seem significant, if this is spread across several ingredients and not properly accounted for during formulation, this can result in a product that is deficient in certain nutrients.
2. Mixing
To produce a consistent product, the ingredients must be thoroughly mixed, so it is homogenous. That is, all the ingredients are equally dispersed and there are equal proportions of each ingredient regardless of the location within the mix. While large inclusion ingredients are generally easy to thoroughly mix, smaller inclusion ingredients, such as premixes and individual amino acids, can be more difficult. Not only must the mixing process itself be adequate, but the process used to weigh and dispense these ingredients must be precise and able to accurately handle small weights. Micro-ingredients such as vitamins and minerals, have a small tolerance relative to other nutrients, so a seemingly small error during mixing and/or weighing can result in a nutrient profile that is very far off from where it was formulated, and in some cases this may be unsafe.
3. Processing
It is well-known that processing can affect the nutrient profile of ingredients and finished products, particularly with heat-sensitive nutrients such as vitamins.5 For example, previous research has demonstrated a considerable decrease in the amount of vitamin A, vitamin D, and thiamine when extrusion temperatures were increased from 100 to 180°C.5 Variables such as temperature and retention time will vary from plant to plant and lot to lot. This certainly leads to inherent variation in the nutrient profile of the finished product. If the process is not properly controlled, or if processing losses are not appropriately controlled for, this can result in a diet deficient in certain vitamins even if the diet was formulated to meet the requirement.
Selecting a food
While there are many areas where error can creep into pet food manufacturing, good manufacturers and formulators will take precautions to protect against this. In addition to having experienced formulators, providing a buffer for nutrients during formulation, testing ingredients, and analyzing the finished product for nutrients all help to ensure that the food is appropriately balanced when it gets put on the shelf. Additionally, brands that have a strong history of good manufacturing practices can also assist with providing safe food for pets.
References
- Murphy, KM, PG, Reeves, SS, Jones. 2008. Relationship between yield and mineral nutrient concentrations in historical and modern spring wheat cultivars. Euphytica. 163:381-390.
- Acharya, C, P, Sharma. 1994. Tillage and mulch effects on soil physical environment, root growth, nutrient uptake and yield of maize and wheat on an Alfisol in north-west India. Soil Tillage Res. 32(4):291-302.
- Lee, J, DS, Nam, C, Kong. 2016. Variability in nutrient composition of cereal grains from different origins. SpringerPlus. 5(1):419.
- Tran, QD, WH, Hendriks, AF, van der Poel, 2008. Effects of extrusion processing on nutrients in dry pet food. J. Sci. Food Agr. 88(9):1487-1493.
- Yang, P, H, Wang, M, Zhu, Y, Ma. 2020. Evaluation of extrusion temperatures, pelleting parameters, and vitamin forms on vitamin stability in feed anim. (Basel). 10(5).
Follow us on LinkedIn for the latest updates on all things happening here at BSM Partners.
About the Author
Dr. Chuck Zumbaugh works at BSM Partners as an Assistant Manager in Nutrition Services. He has experience in biochemistry, chemistry, software development, and animal nutrition. Outside of work, he enjoys spending time outdoors with his family in Kansas.
This content is the property of BSM Partners. Reproduction or retransmission or repurposing of any portion of this content is expressly prohibited without the approval of BSM Partners and is governed by the terms and conditions explained here.